Porosity in Welding: Identifying Common Issues and Implementing Best Practices for Prevention
Porosity in welding is a prevalent issue that usually goes undetected until it creates considerable issues with the stability of welds. This typical problem can jeopardize the stamina and toughness of welded structures, presenting safety and security risks and causing pricey rework. By recognizing the root triggers of porosity and carrying out reliable prevention techniques, welders can dramatically boost the quality and reliability of their welds. In this conversation, we will certainly check out the vital factors adding to porosity formation, analyze its detrimental results on weld performance, and review the very best techniques that can be adopted to decrease porosity event in welding procedures.
Typical Causes of Porosity
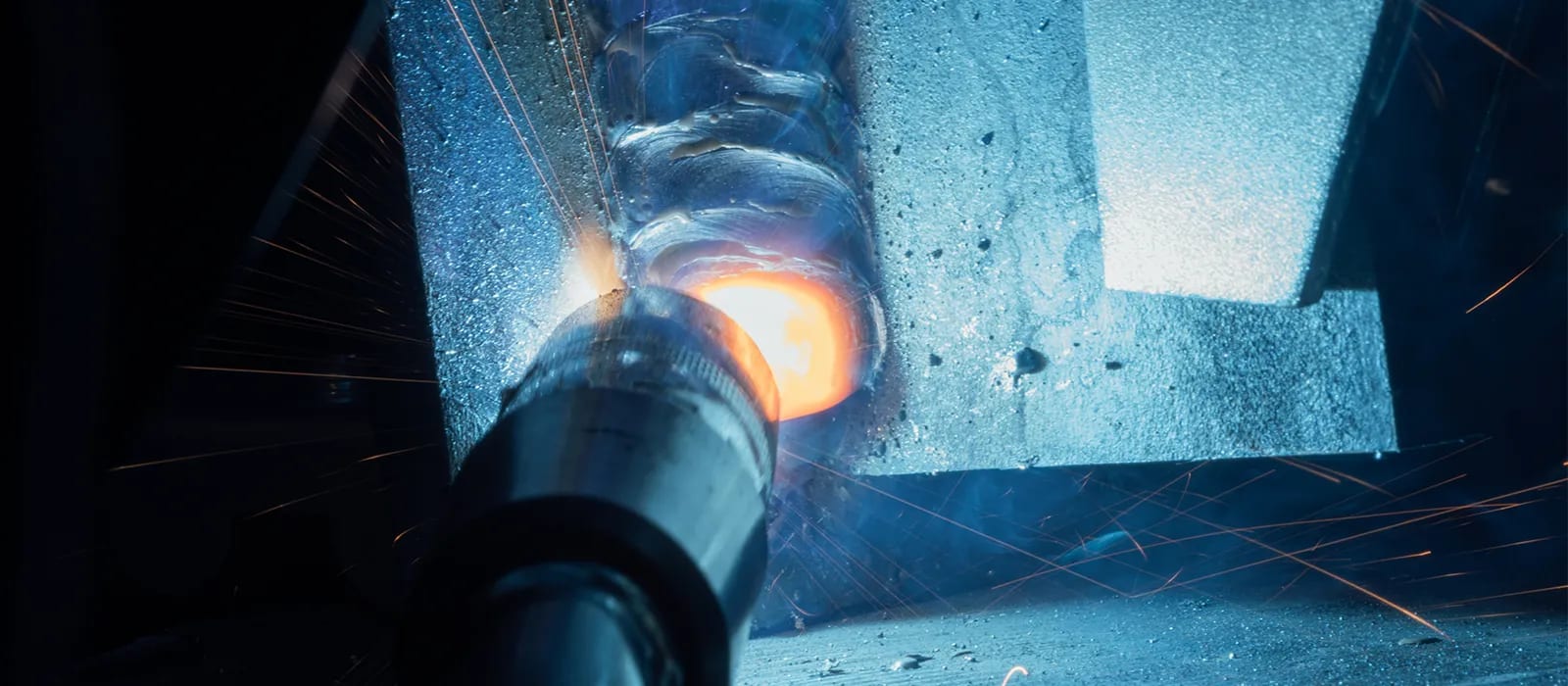
Utilizing dirty or wet filler products can introduce contaminations into the weld, adding to porosity issues. To mitigate these usual reasons of porosity, extensive cleansing of base metals, proper shielding gas option, and adherence to ideal welding specifications are essential methods in attaining premium, porosity-free welds.
Impact of Porosity on Weld Quality

The visibility of porosity in welding can considerably jeopardize the structural stability and mechanical residential properties of welded joints. Porosity develops voids within the weld metal, compromising its general strength and load-bearing capability.
Welds with high porosity degrees tend to show reduced impact strength and lowered capability to warp plastically before fracturing. Porosity can impede the weld's capability to successfully transmit forces, leading to early weld failing and potential security risks in vital frameworks.
Ideal Practices for Porosity Avoidance
To boost the architectural stability and top quality of bonded joints, what particular measures can be executed to decrease the incident of porosity during the welding process? Making use of the appropriate welding technique for the certain product being welded, such as adjusting the welding angle and weapon position, can better prevent porosity. Routine evaluation of welds and prompt remediation of any concerns recognized throughout the welding process are necessary methods to protect against porosity and create top quality sites welds.
Importance of Correct Welding Methods
Implementing proper moved here welding methods is paramount in ensuring the architectural stability and top quality of welded joints, building upon the structure of efficient porosity prevention steps. Welding methods straight affect the general stamina and sturdiness of the welded framework. One crucial facet of proper welding techniques is preserving the correct warm input. Too much warm can bring about raised porosity due to the entrapment of gases in the weld swimming pool. Conversely, insufficient warmth might result in insufficient fusion, producing possible powerlessness in the joint. In addition, using the ideal welding parameters, such as voltage, current, and take a trip rate, is vital for attaining audio welds with minimal porosity.
Furthermore, the selection of welding process, whether it be MIG, TIG, or stick welding, must align with the certain requirements of the job to make certain optimum results. Correct cleansing and prep work of the base metal, along with choosing the ideal filler product, are likewise important elements of skillful welding techniques. By sticking to these finest practices, welders can decrease the danger of porosity development and generate premium, structurally audio welds.

Evaluating and Quality Control Procedures
Testing treatments are crucial to detect and protect against porosity in welding, making certain find the stamina and sturdiness of the last item. Non-destructive screening methods such as ultrasonic testing, radiographic testing, and visual examination are generally used to recognize possible flaws like porosity.
Performing pre-weld and post-weld assessments is also essential in maintaining quality assurance criteria. Pre-weld evaluations entail confirming the materials, devices setups, and sanitation of the workspace to avoid contamination. Post-weld inspections, on the other hand, analyze the final weld for any problems, consisting of porosity, and confirm that it satisfies defined requirements. Carrying out a thorough quality assurance strategy that consists of extensive screening procedures and examinations is extremely important to lowering porosity problems and making sure the overall high quality of bonded joints.
Verdict
In conclusion, porosity in welding can be an usual concern that affects the quality of welds. By identifying the typical root causes of porosity and applying finest methods for prevention, such as proper welding techniques and screening steps, welders can ensure excellent quality and dependable welds. It is important to prioritize prevention methods to decrease the incident of porosity and keep the honesty of welded frameworks.